OUR GLOBAL CHALLENGES Nihon Shinkan Co., Ltd.
Wielding its competence in a process known as aluminum drawing, the company began licensing its technology overseas in the 1990s. In order to facilitate business expansion not only in Japan but in Thailand as well, the company is one of the few in the industry with an integrated manufacturing system in which the entire process is done in-house.
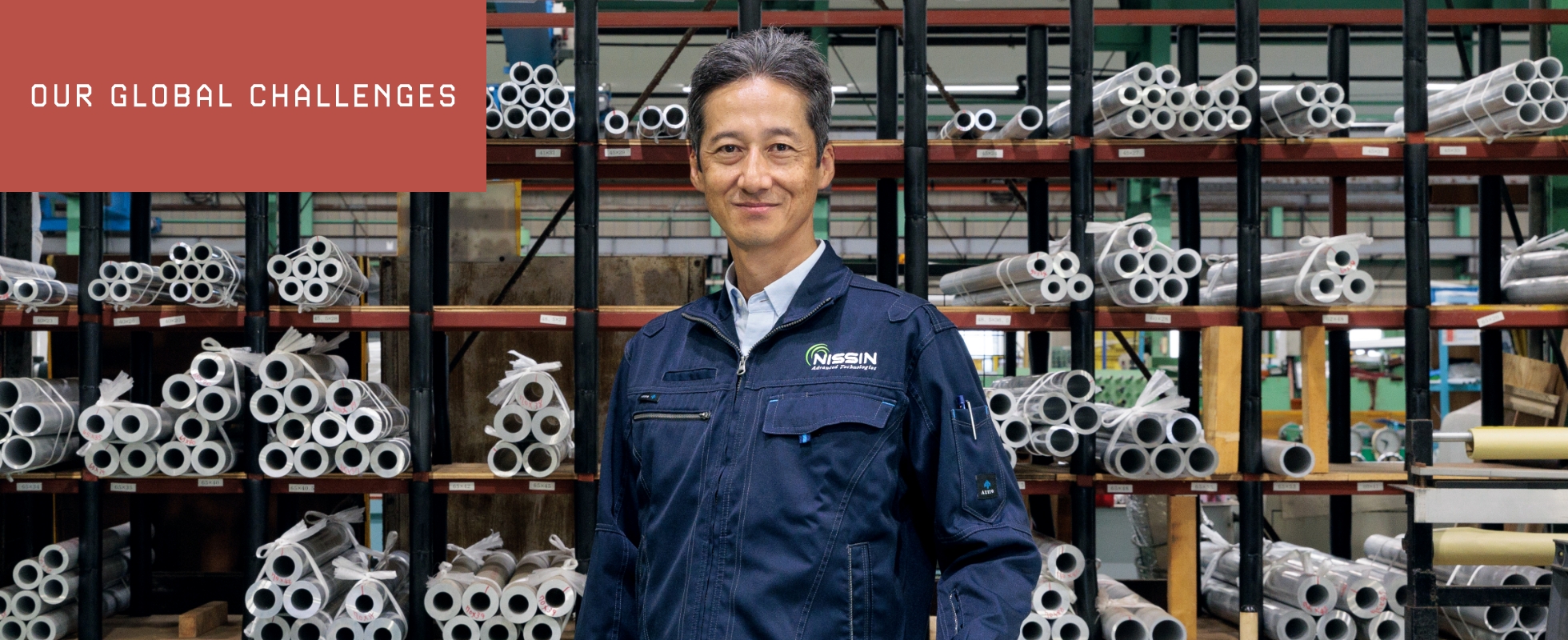
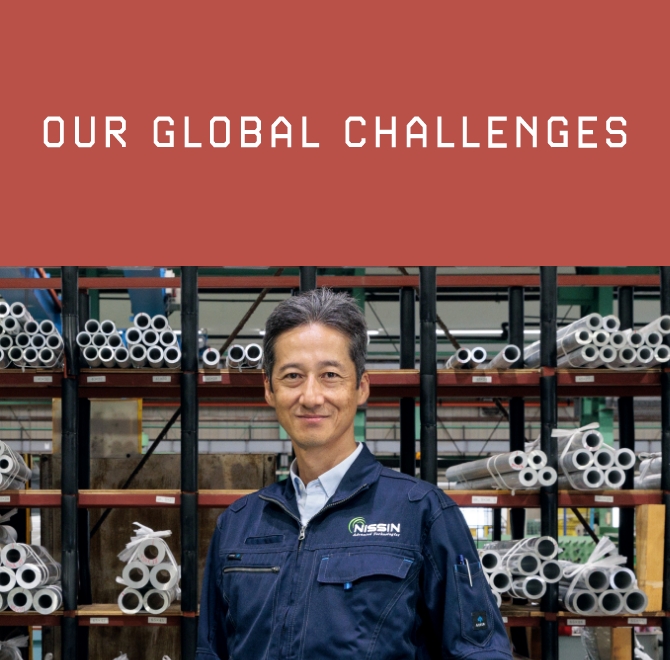
President, Nihon Shinkan Co., Ltd.
HOSONUMA Naoyasu Joined Sony Corporation after completing a master’s degree in science and engineering at the Tokyo Institute of Technology. Joined Nihon Shinkan, which was founded by his father, in 2001 and became president in 2008. Under the slogan of “Aiming to be a ‘small but world-leading company,’” he is working to develop new domestic and overseas sales channels.
Processing aluminum pipes at production centers in Saitama, Fukushima, and Thailand
Aluminum is one of the lightest metals in existence, and has outstanding corrosion resistance, electrical conductivity, and thermal conductivity. It can reduce the weight of components while maintaining the required strength, and can also be fairly easily formed into complex configurations used in various products. These include AT spool valves (parts for adjusting hydraulic pressure in automobile automatic transmission systems), components of automatic rear doors for vehicles, camera lens barrels, and photoconductor drums in copiers.
Headquartered in Niiza City, Saitama Prefecture, Nihon Shinkan specializes in aluminum processing, including the drawing, processing, and surface treatment of aluminum pipes. Manufacturing centers are located in its headquarters, Fukushima (Nishigo Village), and Thailand. It has established an integrated manufacturing system to handle the entire process from procurement of materials to product assembly using advanced technological capabilities that have won praise from the Japanese government as “world-leading aluminum processing technology.”
According to its president, HOSONUMA Naoyasu, “Flexible technological skills and responsiveness are crucial in materializing our client’s ideas. Our company’s strengths are our ability to deliver consistent quality in mass production and to accommodate needs for integrated manufacturing, which lowers total costs.” Since its foundation in 1967, the company has been enhancing technologies that specialize in drawing, in which the diameter and cross-sectional area of aluminum pipes are reduced by passing them through drawing dies at room temperature.
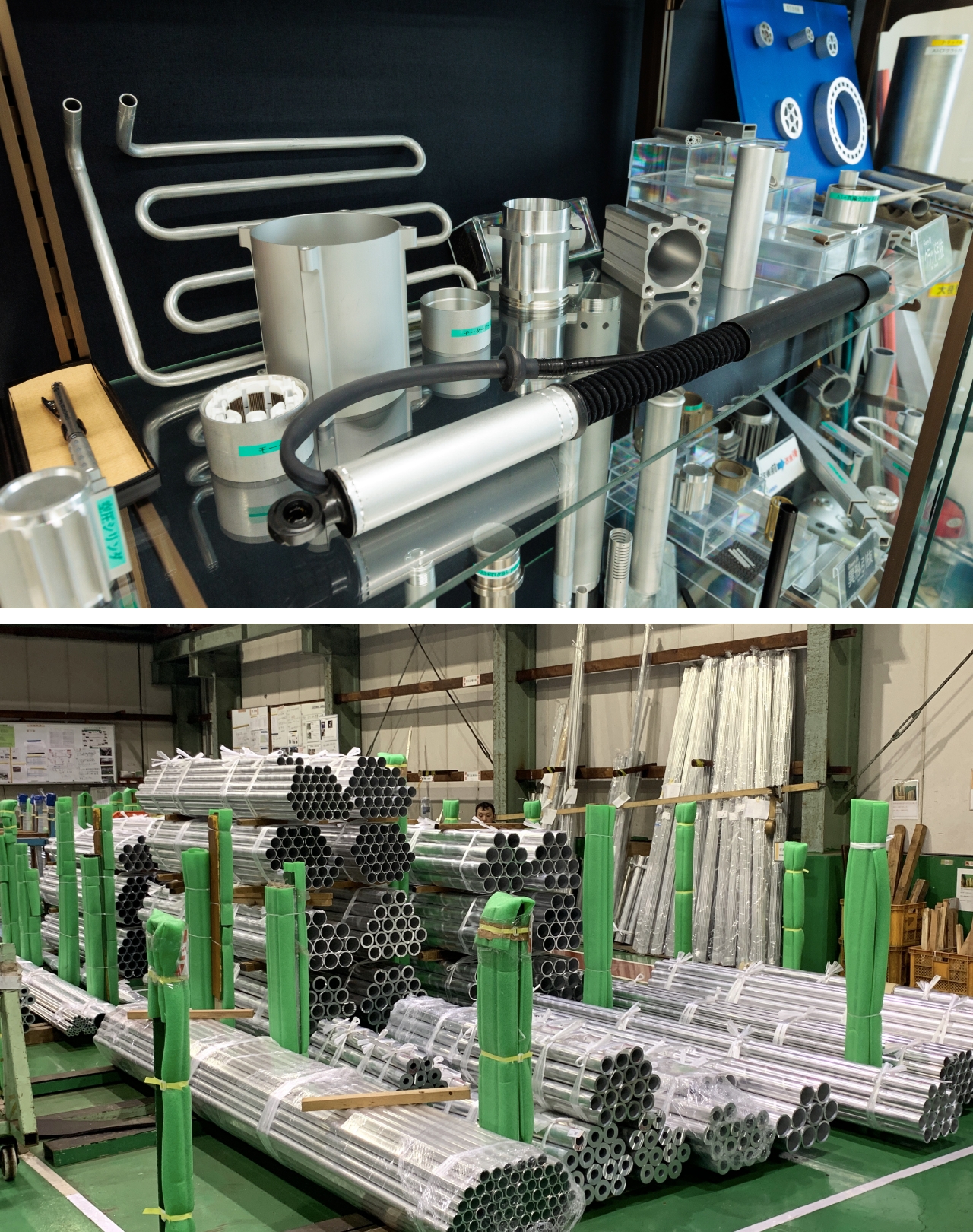
With high-level specialized technologies and a system capable of mass production, the company manufactures aluminum components for a wide range of fields from precision instruments to household appliances. Camera lens barrels and other products are stacked in the factory.
However, if the company rested on its laurels, its potential growth would eventually reach its limits. With this in mind, in 1985 former President HOSONUMA Tetsuo established Alma Co., Ltd., an aluminum surface treatment plant for hard anodic oxidation that improves resistance to metal corrosion. This laid the foundation for Nihon Shinkan to be one of the few companies in the industry that handles the entire process from procurement of materials to metal processing and surface treatment.
Even after his son took over the business in 2008, this thinking outside the box for future business prospects has remained strong. HOSONUMA says, “We do our best to not turn down customer requests,” he says, “and by taking on challenges to meet their needs, new possibilities are born. Recently, we have even begun assembling and packaging products in-house.”
Consistent mass production capability for opportunities in areas other than industrial equipment
Nihon Shinkan’s work covers multiple sectors, from office equipment to camera parts, automotive parts, agricultural and forestry equipment, household goods, railroad parts, and even pipes to drill through Antarctica’s thick ice sheet.
The National Institute of Polar Research launched an ambitious project in Antarctica to shed light on Earth’s crustal movements and the mechanism of climate change by drilling deep into 1 million-year-old ice core and analyzing the atmospheric components found inside. Deeper ice core drilling was made possible by a proprietary outer casing manufactured in 2003 by Nihon Shinkan. This not only contributed to the future of humanity, but also showed the world Japan’s advanced technological capabilities.
According to HOSONUMA, the company’s big turning point came with its production of parts for cleaning tools. Mass production requirements were met with peak monthly shipments surpassing 1 million units. This advancement into a new field was made possible by the company’s reputation of having successfully produced more than 2 million photoconductor drums a month (the third largest share in the world).
“Manufacturing per se is not difficult. But it is a totally different matter when you have to consistently make 500,000 to 1 million units a month while maintaining quality,” he says, recalling that this experience broadened the perspectives of all the employees and helped drive the company’s subsequent growth.
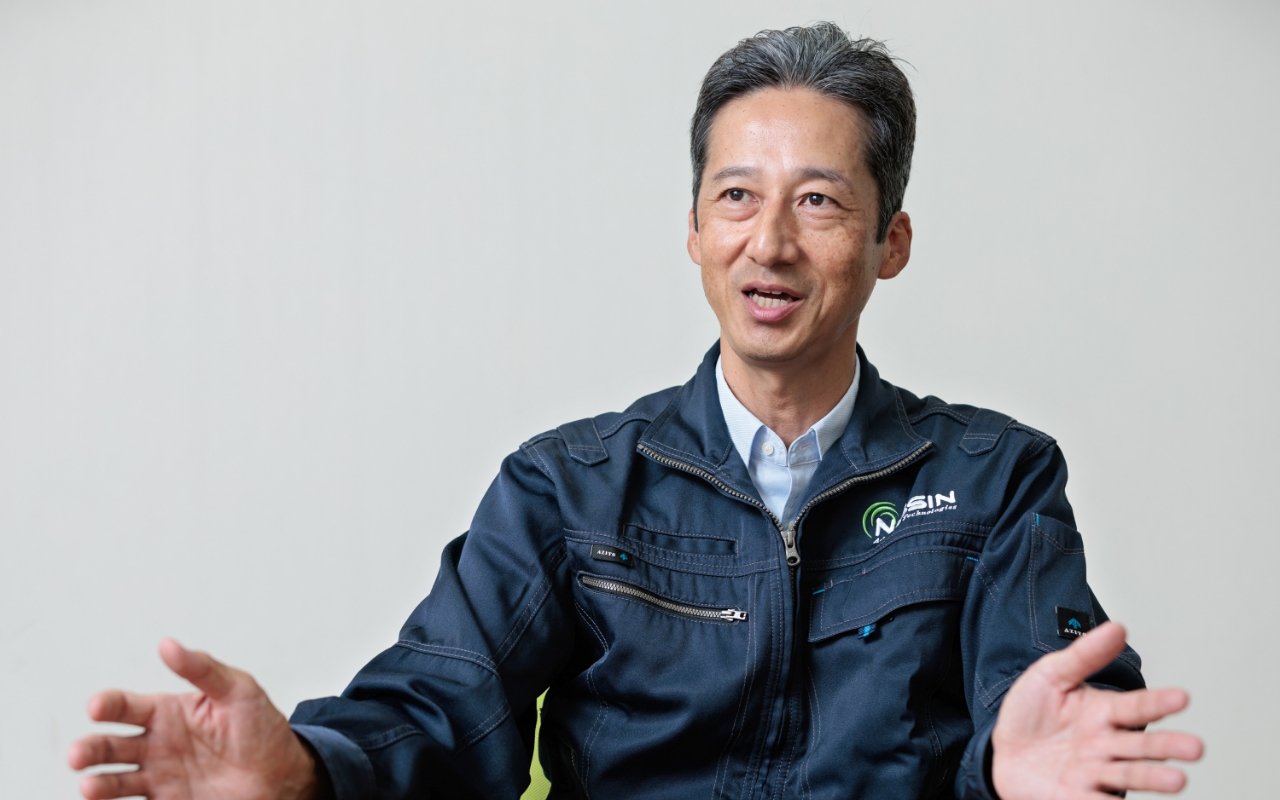
President HOSONUMA Naoyasu says, “do our best and not turn down customer’s re-quests,” and he continues to take on new challenges.
Understanding local production needs with the aim of expanding revenues and sales channels in Thailand
Another management strategy that has been carried forward since the founding of the company is a focus on overseas markets. In the beginning of the 1990s, office automation equipment, one of Japan’s leading areas in manufacturing, caught the attention of European countries. The high-tech capabilities of Nihon Shinkan were recognized here, and it began licensing its technology to a British company. That experience proved extremely useful in its later advancement into the Thai market.
In September 2012, Nihon Shinkan established its Thai plant in Ayutthaya Province. Back then, there were hardly any Japanese aluminum drawing companies with cutting-edge technologies operating in Thailand. The deciding factors in choosing Thailand were a better industrial infrastructure than other Southeast Asian countries, ease of raw material procurement, and a good labor force. And with many Japanese affiliates located there, business opportunities could be expanded.
According to HOSONUMA, “The Japanese economy was in a slump due to the global financial crisis triggered by the collapse of Lehman Brothers, making Thailand’s vitality very attractive. The atmosphere there was similar to that of Japan during the post-war rapid economic growth era, and I acutely felt that the know-how we had cultivated up to now would be put to good use here.” The Thai factory celebrated its 10th anniversary in 2022, and a second factory was completed in 2023. The company continues to expand its market, centering on Japanese-affiliates.
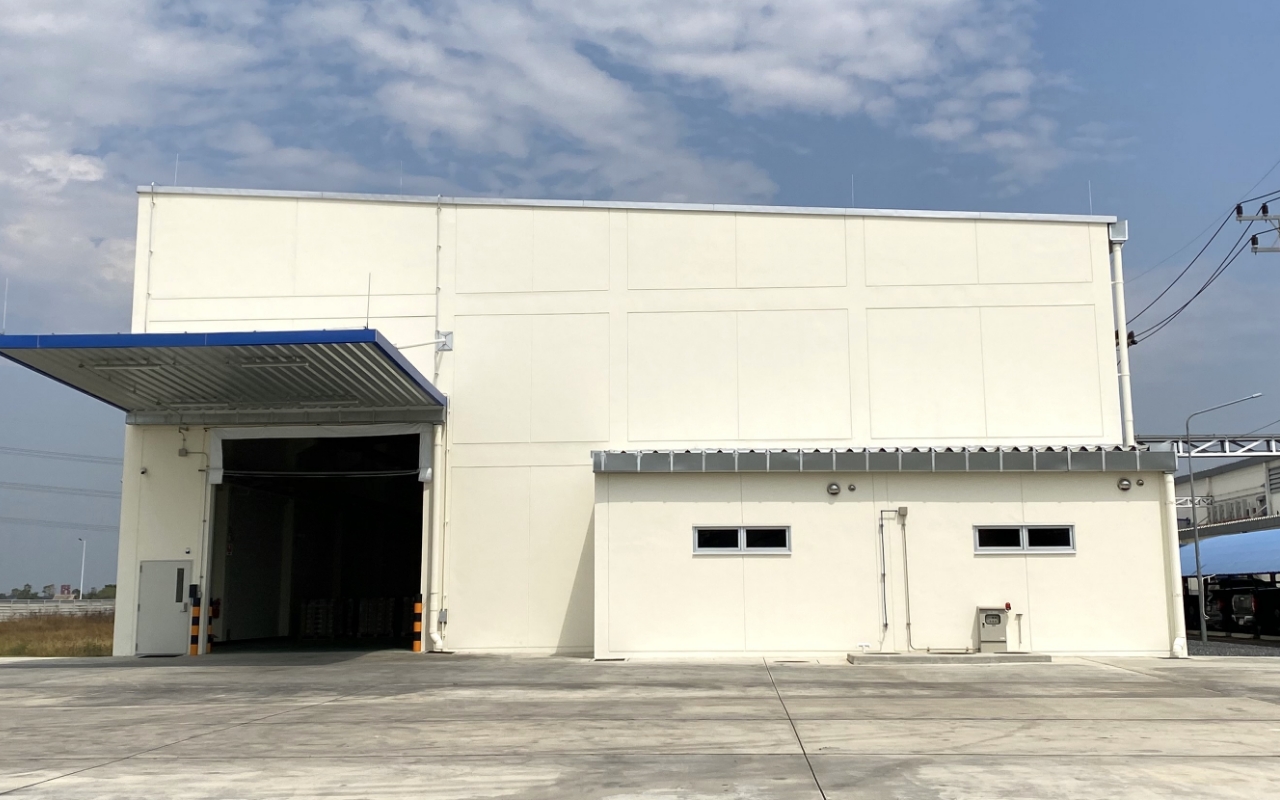
The second plant in Thailand was completed in 2023. The site is more than 35,000 square meters, and employees number more than 100. In addition to office automation equipment parts, new orders for small electronic device parts will be handled here.
Overseas expansion has given the company a broader view of the global market through access to a great deal of information that could not be obtained in Japan alone. Clients would provide information that is only known locally because “your company has a factory overseas.” That is the big difference between a company that has taken steps forward, however small, and one that only has the intention to do so.
While Nihon Shinkan does face issues particular to small and medium-sized enterprises such as developing global human resources, it does not intend to stop moving ahead. The company is responding to a wide range of customers’ requirements through research and development at the Technology Development Center, which was established in Japan in 2014. It also aims to expand its business in December 2023, centering on agricultural and forestry equipment, by utilizing its integrated manufacturing system in Thailand. “It is our job to help companies commercialize their products. We hope to continue to expand our technologies by leveraging our strengths in accommodating requests that go beyond drawing.”
The goal is to become “a small but world-leading company,” Nihon Shinkan will continue to meet client needs by balancing specialization and diversification, and promoting long-term technological development.
Nihon Shinkan Co., Ltd.
1967 | Company established |
---|---|
1976 | Fukushima and Shirakawa plants completed |
1985 | Established Alma Co., Ltd. (hard anodic oxidation plant) |
1991 | Started licensing technology to a British company |
2003 | Developed and manufactured outer casing for Antarctic ice sheet drills |
2012 | Established NIHON SHINKAN (THAILAND) Co., Ltd. |
2014 | Established the Technology Development Center |
2023 | Completed its second plant in Thailand |
Since March 2018, loan agreements have been signed with Nihon Shinkan’s Thai affiliate, NIHON SHINKAN (THAILAND) Co., Ltd., for loans up to 99 million Thai baht (JBIC portion). Co-financed with the Musashino Bank and Saitama Resona Bank. This supports the manufacturing and marketing of aluminum products in Thailand, and contributes toward maintaining and improving the international competitiveness of Japanese industry.